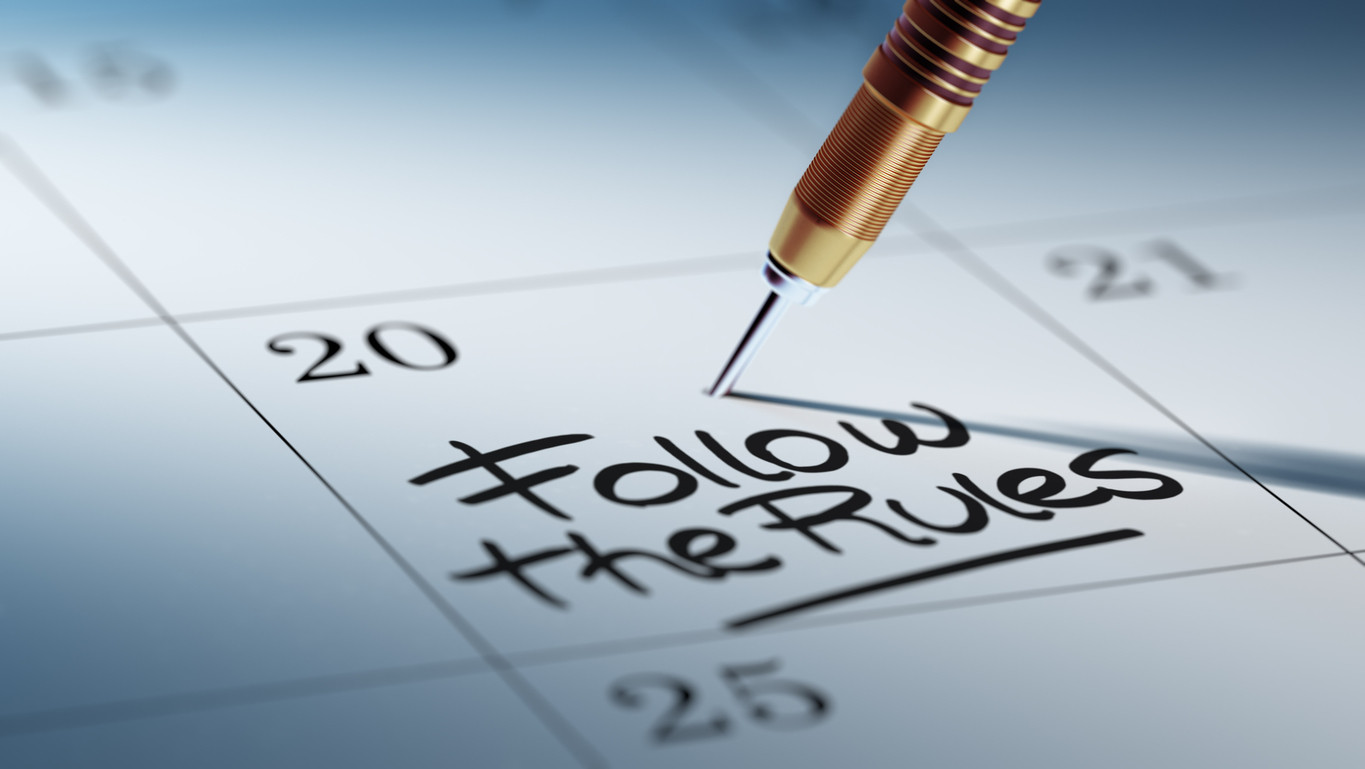
Rule One: Complex profiles = Complex Details = Complex installations
Often, waterproofing can become complex when, in fact, a simple solution could be found if the construction sequence and proposed substrates can be understood fully. Some systems require multiple laps and joints, some can be vulnerable to damage whilst for others, maintaining waterproofing integrity between different substrates can be difficult.
When collaborating with our clients on waterproofing strategy we always look to design out complexity where possible.
Understanding how the building may move and allowing for different movement will help get to the most efficient waterproofing design. For example one consideration may be the use of a liquid applied system that will follow contours and protect edges as necessary.
Another key element is to understand the sequence of build as interfacing with other trades often presents the greatest challenge down the line.
Rule Two: Penetrations increase the risk of leaks
Penetrations such as base plates, gully outlets and services also bring complexity, breaking the integrity of waterproofing and making them vulnerable to water ingress or differential movement. In these situations it is worth minimising them where possible, designing in multiple layers of defence and allowing for differential movement.
It is advisable to grout or box-in the base plates using high build repair mortar. This provides a continuous surface, which makes waterproofing installation far simpler. Other successful techniques include ensuring the membrane can bond to different substrates, for example concrete and steel, so that continuity at these sensitive interfaces is robust. Furthermore, we recommend the use of resin anchoring grouts where post fixing through liquid waterproofing is unavoidable.
When it comes to service penetrations, the pipe or conduit materials will differ from the substrate that they pass through. It is important to select a material, which bonds to both materials, for example concrete wall and plastic pipe, and also deals with the potential differential movement between the two.
Rule Three: Maintain waterproofing continuity over construction joints
Construction joints are subject to thermal and structural movement so specification of products with good crack bridging capability is one way forward. A flexible product will accommodate some movement but it may not be enough, so it is also prudent to take in to account differential movement too. By checking the movement capabilities of the system you will be able to ascertain if reinforcement is necessary. When applying liquid waterproofing systems, it is always recommended to debond the system over the movement joint.
Rule Four: Movement joints are at risk of water ingress, so specialist products are required
To avoid water ingress, understanding the movement dynamics of the joint is key. It is advisable not to bridge a movement joint with a membrane - a specialist system such as Radflex is required. Locate this in an upstand (podium) and use falls to run water away from the movement joint (podium) where possible.
Rule Five: Waterproofing sectional detailing must be sequential
One of the crucial rules is not to design sectional details in isolation, always check sequencing. Waterproofing adjacent sectional details will help to maintain continuity and importantly help to avoid unbuildable details.
Rule Six: What’s more important, a product’s attributes or its limitations?
Understanding product limitations is essential to avoid problems later in the build.
Assessing how susceptible a product is to the following factors should help to determine whether it’s fit for purpose:
Site conditions and program?
- Ensuring waterproofing systems are successful is not just down to the product itself but the communication surrounding the process from start to finish. Good lines of communication and supervision, appropriate protection and good site housekeeping all contribute to an effective installation.
Weather conditions during use?
- Some systems are not designed for long-term exposure and performance can be impaired. Products may degrade if exposed to UV or if they become wet or saturated so be sure to check any limitations.
Poor workmanship?
- Equally poor application can compromise integrity. Assess the competence of your contractor or operatives, as standards may not always be consistently high. They should offer an insurance-backed 10-year plus warranty with their workmanship. For more specialist material applications, it’s always sensible to select a specialist waterproofing contractor. Ensure products such as liquid applied coatings are applied as published and in accordance with manufacturer guidelines. Over application leads to failure so build up in multiple coats if required. Testing waterproofing integrity is essential where possible with thorough inspection and sign off, completing the process.
Damage on site?
- Membranes and coatings are vulnerable to damage, some more so than others, it often happens that following trades are not made aware and damage to the waterproofing means its integrity is broken
It is also worth giving consideration to a product’s compatibility, repairability and its service life.
Getting it right at the critical detail stage is essential to the success of a waterproofing scheme. If you’re in any doubt contact a waterproofing design specialist like RIW at the earliest stage. RIW can support with attendance at design meetings, project specific detailing, construction drawings and project delivery protocol.
For more information on getting the critical detail right, contact our sales team on 01753 944200.